The Landscape of Motor Technologies in the Semiconductor Equipment Market
Whether it is Frontend or Backend manufacturing technology, the entire semiconductor Industry is striving to reach movement performances near the physical limits. The semiconductor field is growing with its expectations driven by AI & Advanced Packaging to ensure the production of high-performance memory devices. This stretches the performance required from every component involved in motion technology, including motors.
March 19, 2025
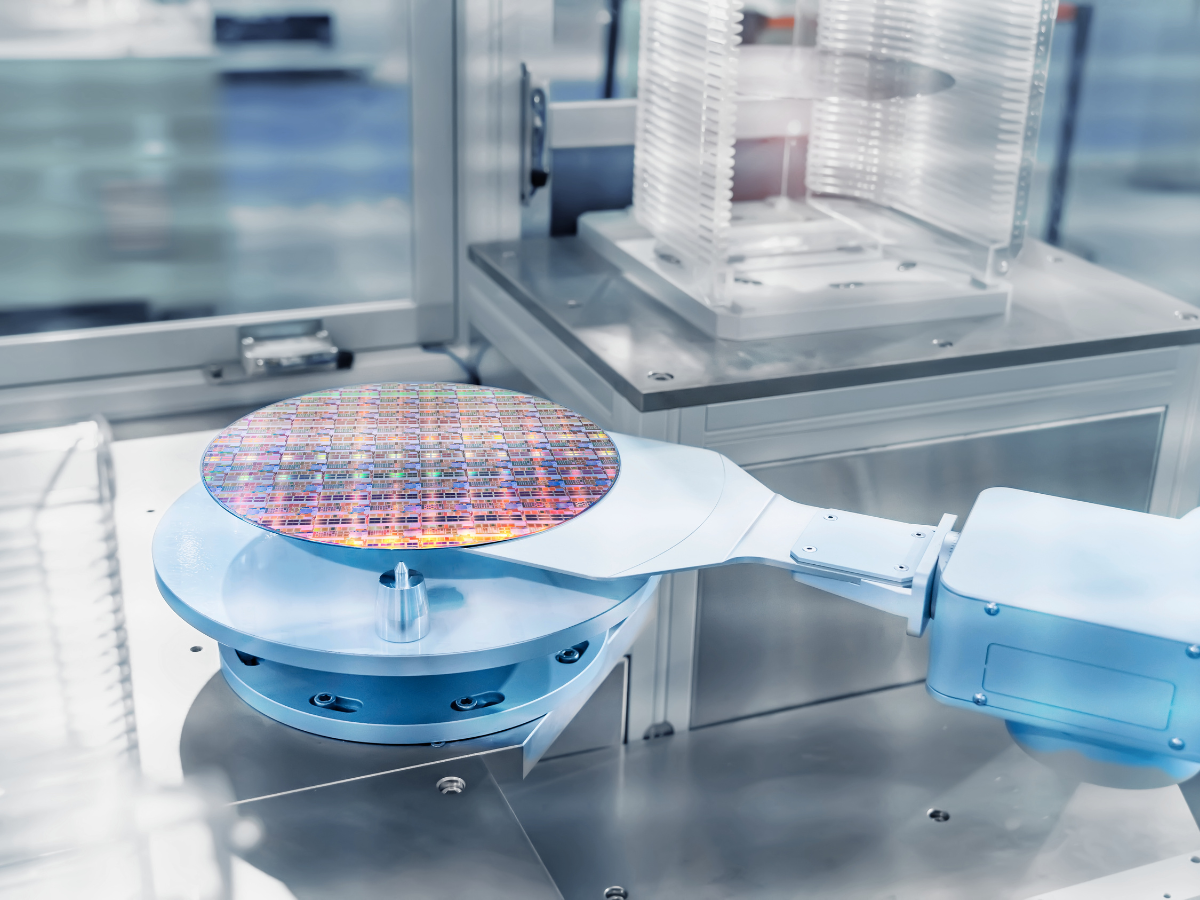
Motion in the Semiconductor industry: Applications and requirements
The semiconductor industry is characterized by extremely high precision requirements, demanding cutting-edge technologies for motion control and positioning systems – for both linear and rotary movement patterns. The overall accuracy requirements in combination with the highest dynamics are bringing complexity to the motor technologies used.
In semiconductor manufacturing, precision and reliability in all motion tasks are critical for the processes of the machine builders, such as wafer handling, wafer cleaning, photomask alignment, lithography up to inspection.
Wafer Processing and Alignment
Semiconductor wafers require precise positioning during the different manufacturing processes like etch, deposition, spin cleaning and lithography. But the focus is not only on precise positioning, accurate and smooth movement during the processes is also crucial.
Especially in the etching and deposition processes, smooth and accurate motion which ensures stability during the production steps. This minimizes vibrations, positioning errors, and enables more effective and shorter production times. This requirement is crucial to achieve and maintain the integrity of sub-micron to Nanometer structures on wafer surfaces. So called “on wafer performance” will be significantly increased which is a main target for all leading players within the industry to ensure highest wafer quality.
.png)
Photomask and Reticle Handling
During the production of integrated circuits (ICs), photomasks and reticles must be processed and handled with extreme care to avoid contamination and misalignment. Backlash-free motion ensures that the patterns on the photomasks are transferred accurately during the exposure process. In motion technologies, one of the contamination sources is wear. To avoid wear, direct drive motion technologies are preferred. These feature optimized heat dissipation and are easy to integrate and encapsulate due to the very compact mounting envelope.
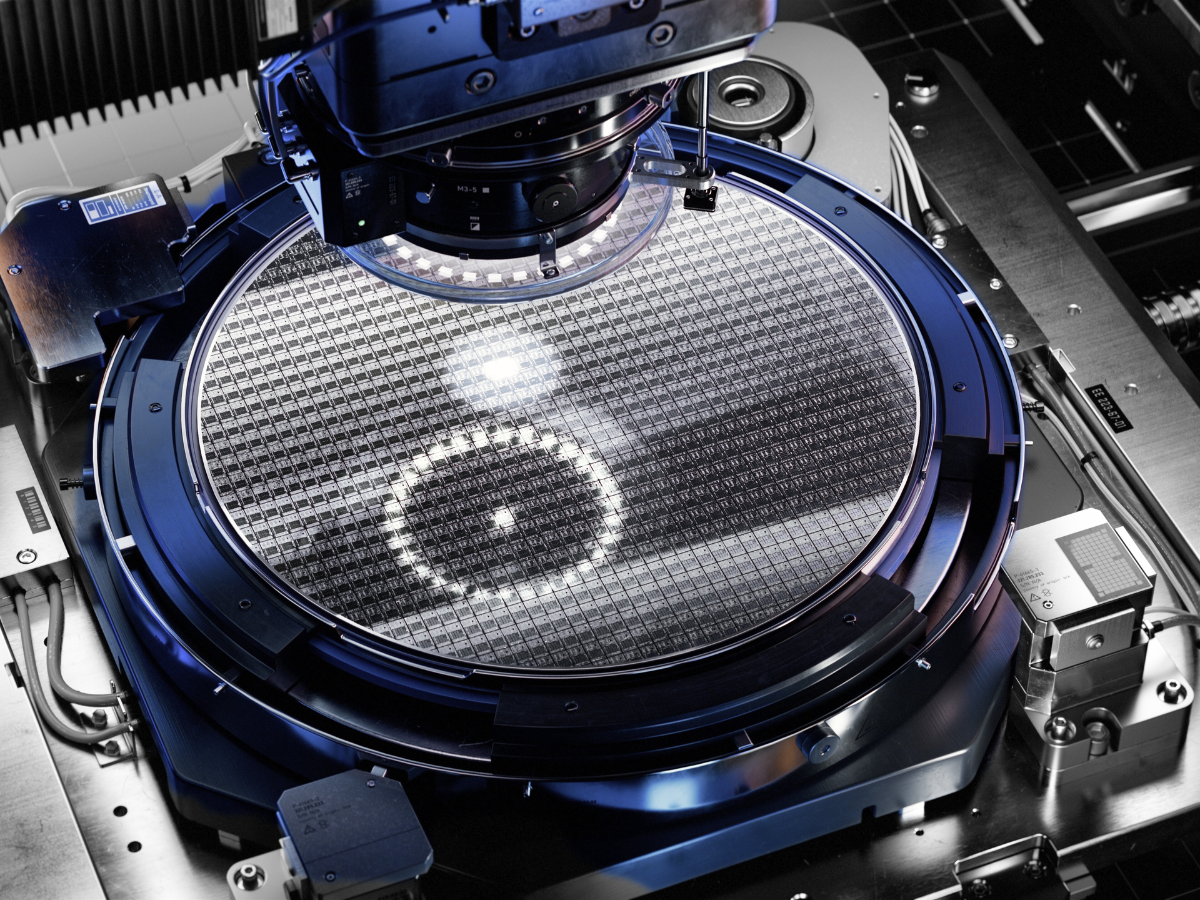
Inspection Equipment
In the field of Quality Assurance after the production processes, especially scanning electron microscopes (SEMs), are benefiting from the smooth operation. The quality and efficiency of inspection processes depend strongly on sensors that are either moving or scanning the wafer moving, thanks to the motion system. Therefore, machine builders need to implement highly precise motion technologies, to meet the stringent quality standards required in semiconductor production.
.png)
Motor requirements in the Semiconductor Industry
Low Cogging Torque
One of the most significant challenges in the applications mentioned above is the cogging torque - a phenomenon common in slotted motors where the interaction between permanent magnets and stator slots causes irregular motion. This issue can be compensated by software mapping or filtering of the electronics, however it is not always working in the expected way and requires certain compromises and skills. Especially not if the running performance is of highest interest.
High Torque Density
Semiconductor fabrication lines require high torque density to remain as compact as possible due to the high costs of clean room space. This way, encapsulation and integration are also easier, and more cost and performance optimized.
Enhanced Efficiency and Reliability
Reliable motor technologies lead to improved energy efficiency and longer operational lifespans, reducing downtime and maintenance costs—a crucial factor in high-volume semiconductor manufacturing. In parallel the sustainability and the necessary green footprint aspects are directly enhanced.
Improved Dynamic Response
High acceleration and deceleration with minimal overshoot is critical in applications requiring rapid movement changes. This dynamic performance is requested by most operations on wafer transport and alignment during lithography. This is possible in motors with low inductance combined with high switching frequencies (PWM).
Peak torque performances
Related to the topic above, high acceleration means also high peak torque for motor technologies.
Slotless and Slotted Torque Motors in Semiconductor equipment
While both slotless and slotted torque motors are common for rotational motion, there are key differences in design and performance. Here we touch upon the differences that are relevant to the semiconductor industry, for more, please read here.
Design Architecture
Slotted torque motors incorporate stator slots that hold the windings, which inherently introduces periodic variations in the magnetic field causing the so-called cogging torque. In contrast, slotless motors have windings that are embedded in a continuous surface, thereby reducing magnetic ripple and enhancing smoothness of operation.
Torque Ripple and Motion Smoothness
Slotted motors typically exhibit noticeable torque ripple due to the cogging effect, which can lead to vibrations and less precise control. The slotless design minimizes these irregularities, making it particularly beneficial for applications requiring fine control and minimal disturbance, such as in semiconductor manufacturing.
Heat Dissipation and Efficiency
Slotted motors tend to offer better heat dissipation than slotless motors. However, new generation slotless motors produced with new methods, close the gap between the two technologies significantly. In cases where a slotted design is used at saturation or beyond, slotless motors may offer better efficiency overall.
Cost and Complexity
Generally, slotted torque motors can be less expensive to manufacture due to their simpler winding structures. However, the cost benefits may be opaqued by the additional need for advanced control systems to mitigate cogging effects. In high-precision semiconductor applications, the improved performance and reliability of slotless motors often justify their little higher initial cost.
FiberPrinting™ and SlimTorq™ Motors from Alva Industries
Slotless torque motors represent a significant technological advancement in the field of precision motion control. However, sometimes they do not offer enough torque density to achieve the required results and can be difficult/expensive to manufacture. The Alva SlimTorq™ FiberPrinted slotless motors are the solution to those challenges, and therefore a great choice for Semiconductor applications.
.png)
The inherent advantages of low cogging torque, high torque density, improved dynamic response, and enhanced efficiency make them particularly well-suited for environments that demand exceptional precision. In comparison to slotted torque motors, the benefits offered by slotless designs in terms of motion smoothness and operational reliability are pivotal in meeting the rigorous demands of semiconductor manufacturing. As the industry continues to evolve with increasing miniaturization and performance expectations, the adoption of FiberPrinted slotless torque motors, and SlimTorq™, is poised to grow, driving further innovation and efficiency in semiconductor processing technology through:
- The thinnest (Highest ID/OD ratio)
- Zero Cogging and extremely low torque ripple
- High Motor Constant (Km)
- Scalable design and manufacturing
To learn more about Alva SlimTorq™ motors and their applications in semiconductor equipment, visit Alva Industries.
Our motors
All rights reserved ©2025