Slotless Motor vs. Slotted Motor: What is the difference?
Learn the difference between a slotless and slotted motor, how a slotless motor works, their advantages and their applications.
September 4, 2024
.avif)
Slotless and slotted motors are two clearly different electric motor topologies. Their names describe the shape of the electrical steel laminations used in the stator. This article outlines the impact that this shape has on the characteristics of the motor. It is key to understand the differences between these two motor types when selecting the correct electric motor for each application.
What is a Slotted Motor?
In a slotted motor, also called an iron core motor, the laminated steel has iron “teeth”, creating spaces in-between those teeth, also called slots. In a slotted motor, the copper windings are wound around the stator teeth. The steel teeth concentrate the magnetic field within the air gap.
The easiest way to determine the motor topology of a particular mechatronic device is to rotate the shaft to detect the presence or absence of a cogging effect. If a cogging effect is present, the motor is a permanent magnet slotted motor. If not, then it could be a slotless design. This is because iron teeth attract the magnets on the rotor while it is rotating, creating an uneven rotation, called cogging.
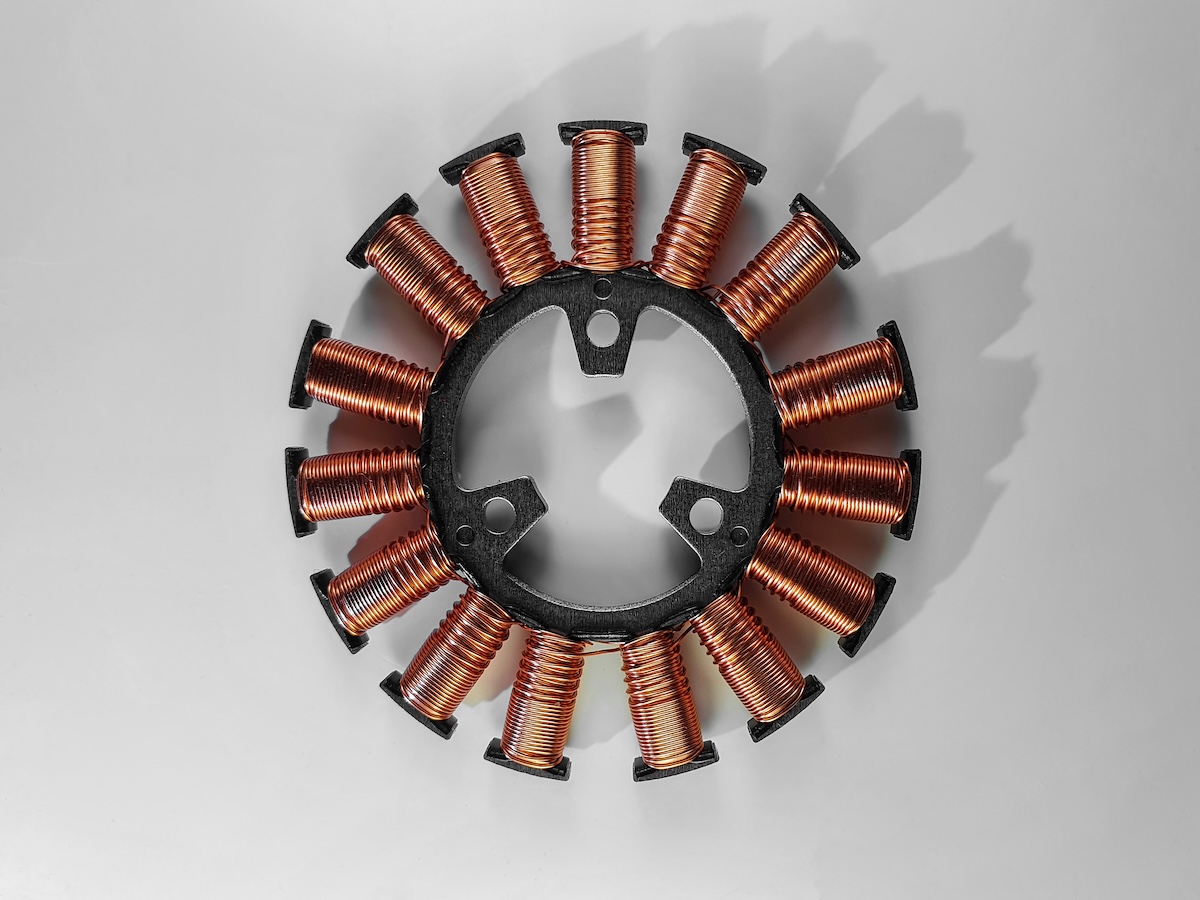
What is a Slotless Motor?
In a slotless motor, the laminated steel is shaped as a smooth ring and placed entirely on the outside of the stator windings. Cogging is not present in slotless motors. In a slotted motor, the copper windings are wound around the stator teeth. In slotless motors, the winding is done differently. Multiple different winding technologies exist for slotless motors.
How does a Slotless Motor work?
Slotless motors function on the fundamental principles of electromagnetic induction, like any other electric DC motor. By applying current, the stator’s windings create a magnetic field that interacts with the rotor’s magnets, inducing rotational movement and generating torque.
The absence of slots in the stator offers several advantages. The elimination of cogging torque, for instance, allows for smoother rotation, making these motors ideal for applications requiring high precision and low vibration. Additionally, slotless motors typically have lower inductance and resistance, which translates to higher efficiency and better thermal management. The smooth core design also allows for more compact motor construction through their thin cross section, enabling higher power density in a smaller footprint.
The electrical steel lamination is also a source of speed-dependent losses. When the motor rotates, the rotor magnets create an alternating magnetic field that interacts with the electrical steel. These stator losses are higher in the parts of the stator laminations that are closest to the magnets. In a slotted motor, the laminations are closer to the rotor, creating higher speed-dependent losses.
Slotless Motor applications
The unique characteristics of slotless motors make them suitable for various applications demanding precision, high speeds, high ID/OD ratio, and high efficiency. Notable applications include:
- Medical Devices: Used in medical imaging systems, surgical instruments, and other devices where precise and reliable movement are essential.
- Aerospace: Valued in aerospace for their lightweight and compact nature, optimizing space and energy efficiency.
- Defence: Many defence applications require high precision, smooth tracking, low weight, and zero cogging, making slotless motors the optimal choice.
- Semiconductor Manufacture: The extreme precision needed to produce semiconductors can be achieved using slotless motors.
- Robotics: Ideal for robotic systems requiring exact positioning and minimal vibration.
- Precision Instruments: Found in optical devices and other instruments where accurate and smooth motion is crucial.
- Marine rim-drives: The large inner diameter results in a large propeller in a rim-driven thruster, increasing efficiency.
.png)
A slotless motor and slotted motor have different strengths and weaknesses
Slotless motors and slotted motors have different strengths and weaknesses:
- Peak torque: Due to their design, slotless motors are almost impossible to saturate, meaning that only the thermal limits restrict their peak torque capabilities. In many applications, the saturation of the steel laminations limits the peak torque capabilities of the slotted motor.
- Inner diameter: Due to the slim steel lamination, a slotless motor has a higher inner diameter to outer diameter ratio than a slotted motor, allowing a more compact design.
- Precision: Slotless motors have zero cogging torque, and more linear torque output for increased torque compared to slotted motors, allowing a higher degree of precision.
- Quicker response time: Slotless motors have lower inductance than slotted motors, resulting in a smaller electric time constant and quicker current response to increased voltage.
- Rotational inertia: Due to the increased distance to the stator laminations, slotless motors have larger magnets than slotted motors, which in turn increases the rotational inertia of the motor.
- Cost: Slotted motors use less magnetic material than slotless motors, which in turn can lead to a lower material cost in production for slotted motors.
- Efficiency: Slotless and slotted motors can both achieve high efficiency if designed well for the application. At very high speeds, slotless motors have lower losses and higher efficiency than slotted motors.
Alva’s FiberPrinting™ technology gives you all these benefits. The graphs below show three comparisons between an Alva slotless motor and a conventional slotted motor, being controlled with an optimal motor driver.
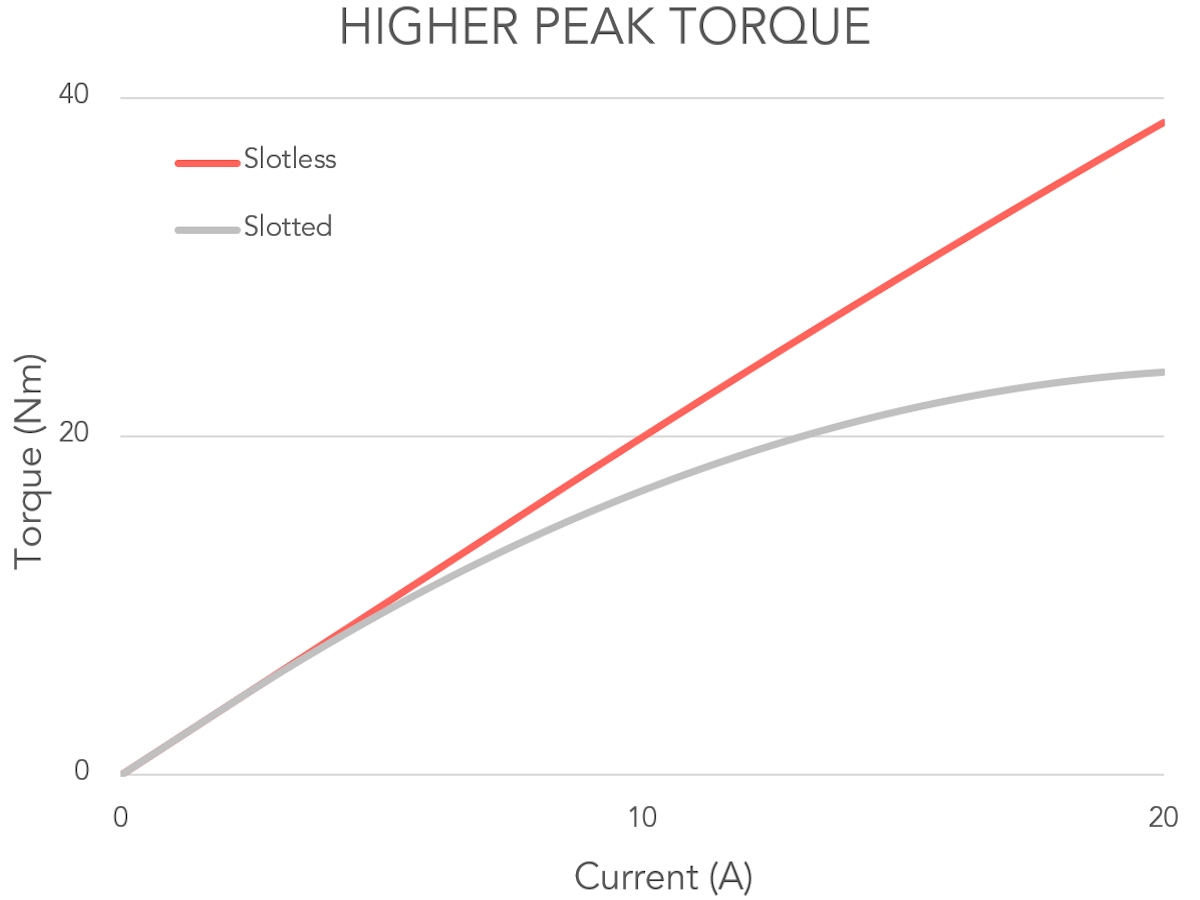

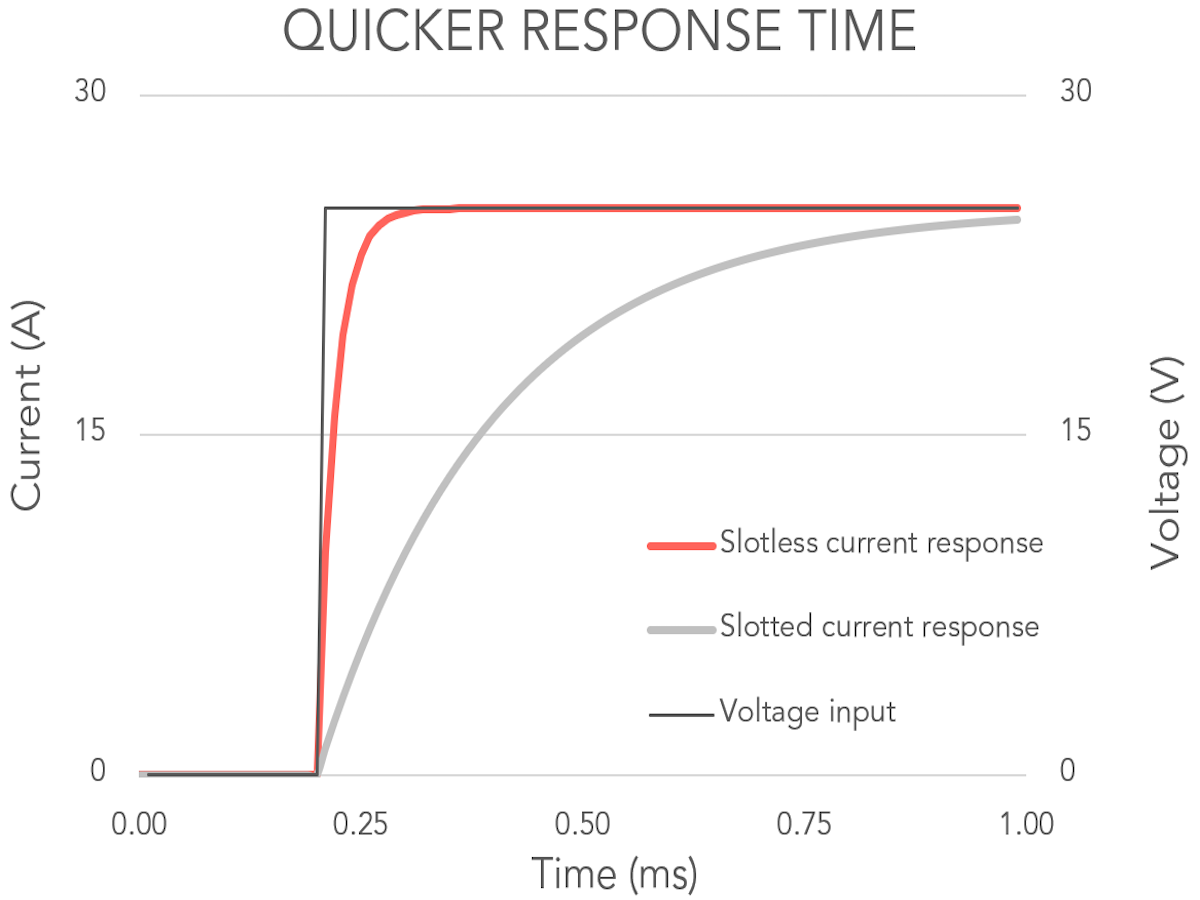
Slotless Precision Torque Motors
Slotless motors excel in applications requiring precise positioning and highly controlled motion. A torque motor is a motor designed optimally for high torque. Using a slotless precision torque motor can increase performance in precision applications due to the zero cogging torque and linear torque-to-current ratio at increased torques. A slotless torque motor virtually never saturates, allowing slotless precision torque motors to achieve very high peak torque.
In fields such as robotic surgery, semiconductor equipment, and high-end imaging systems, the precision delivered by slotless torque motors is often critical. These motors enable exact movements and positioning, which are vital in contexts where even minor deviations can have substantial consequences.
Slotless motors present clear advantages over slotted motors, especially in scenarios demanding high precision, smooth operation, and compact design. A thorough understanding of the differences between these motor types is crucial for selecting the most suitable option for each design.
Nicolas Giraudo
Chief Commercial Officer
Fossegrenda 1,7038 Trondheim, Norway
All rights reserved ©2025