Selecting the Right Motor in Light Robotics Applications
Designing a robotic joint involves careful consideration of many factors. When selecting motors for humanoids, legged robots (or robot dogs), collaborative robots (cobots), and other lightweight robotic applications, each particular design has specific needs.
February 26, 2025
.png)
What is Light Robotics?
Lightweight robots, or “light robots,” are designed to move efficiently over uncertain terrain and typically operate in close proximity to humans or in collaboration with them. These robots need to be agile, mobile, and strong, yet not dangerous. They must also be able to withstand sudden impacts and forces. Humanoids, legged robots, and cobots are some examples of robots that fall under this category.
Humanoids
Humanoids are multi-purpose robots that resemble humans. They are often designed to assist or replace humans in various tasks, such as performing household chores, lifting and carrying objects in factories, or exploring potentially dangerous environments. To mimic human movement, humanoids are equipped with multiple moving limbs and joints, each of which must be powered by motors. These motors need to vary in size, shape, and capability to meet the specific demands of each joint and actuator.
Legged Robots
Legged robots, such as quadrupeds, follow a similar design approach to humanoids, but instead of resembling humans, they resemble animals (e.g., dogs). These robots perform tasks like inspection, exploration, and delivery in environments that may be hazardous or physically exhausting for humans. By assisting human workers, these robots enhance productivity while improving safety. Like humanoids, legged robots require strong, lightweight, and compact motors to maximize operational time and handle demanding tasks.
.png)
Collaborative Robots
Cobots, or collaborative robots, are designed to work alongside humans in shared spaces. They perform tasks such as lifting heavy objects, picking and placing items with high precision and repeatability, or conducting inspections. Since cobots operate near humans, safety is a top priority. Unlike larger robots, which are typically isolated behind protective barriers, cobots must be able to interact with people safely.
Other examples of light robots include exploration bots designed to navigate uncertain terrain, such as rubble after an earthquake or deep inside caves. These robots must quickly adapt and respond to sudden changes in external forces.
The Importance of Torque Density
When designing lightweight robots, the two most critical factors to consider are weight and strength. Both play a key role in selecting actuators for robotic joints. These robots must be lightweight to operate for extended periods while also being strong enough to perform complex tasks. Torque density is the key to achieving this balance.
Joints in these robots are often connected in series, or they must lift their own weight, meaning the motors become part of the moving payload. This creates a compounding effect across multiple stages. A high torque density ensures that each joint can deliver the necessary force while minimizing weight.
Geared Solutions
One way to achieve high torque density is through geared solutions. A gear transmission can increase the torque output of a smaller motor. However, it's also essential to consider back-drivability - the ability of the motor to move in the opposite direction when an external force is applied. For example, if someone grabs a robot arm and moves it in a different direction, the motor/actuator should allow for this movement. This is necessary for ensuring safe interactions between robots and humans, as well as for easy transportation, especially when powered off.
Therefore, transmissions with a low gear ratio are preferred. A low ratio ensures that back-driving forces remain low while allowing the joint to respond flexibly to sudden impacts. Quasi-Direct Drives (QDD) exhibit similar behavior to direct drives but with a low transmission ratio.
Torque Sensing in Robot Joints
Torque sensing is crucial for lightweight robotics because it provides real-time feedback on the torque applied at a specific joint. This feedback enables precise control, safety, and smooth interaction with objects and humans. Dedicated torque sensors are often used for this purpose; however, they add cost, mass, and complexity. If the nonlinearities of the robotic joint can be eliminated, torque can be measured without requiring a separate torque sensor.
Traditional slotted motors have iron teeth that concentrate magnetic flux. These iron teeth create an asymmetric magnetic interaction between the rotor and stator, resulting in cogging torque. In contrast, slotless motors use a simple, ring-shaped laminated core, which eliminates cogging torque and results in more linear behavior. Additionally, slotted motors face saturation issues under high loads.
What is Torque Saturation and Why is it a Problem?
Robots need to be precise, strong, and fast. Under heavy loads, traditional slotted motors can saturate, causing increased losses and a nonlinear current-to-torque ratio. In contrast, slotless motors - without iron teeth - do not experience saturation. This results in a more linear current-to-torque behavior, allowing for higher peak torque and better efficiency, particularly in dynamic applications that require high torque over a wide range of speeds.
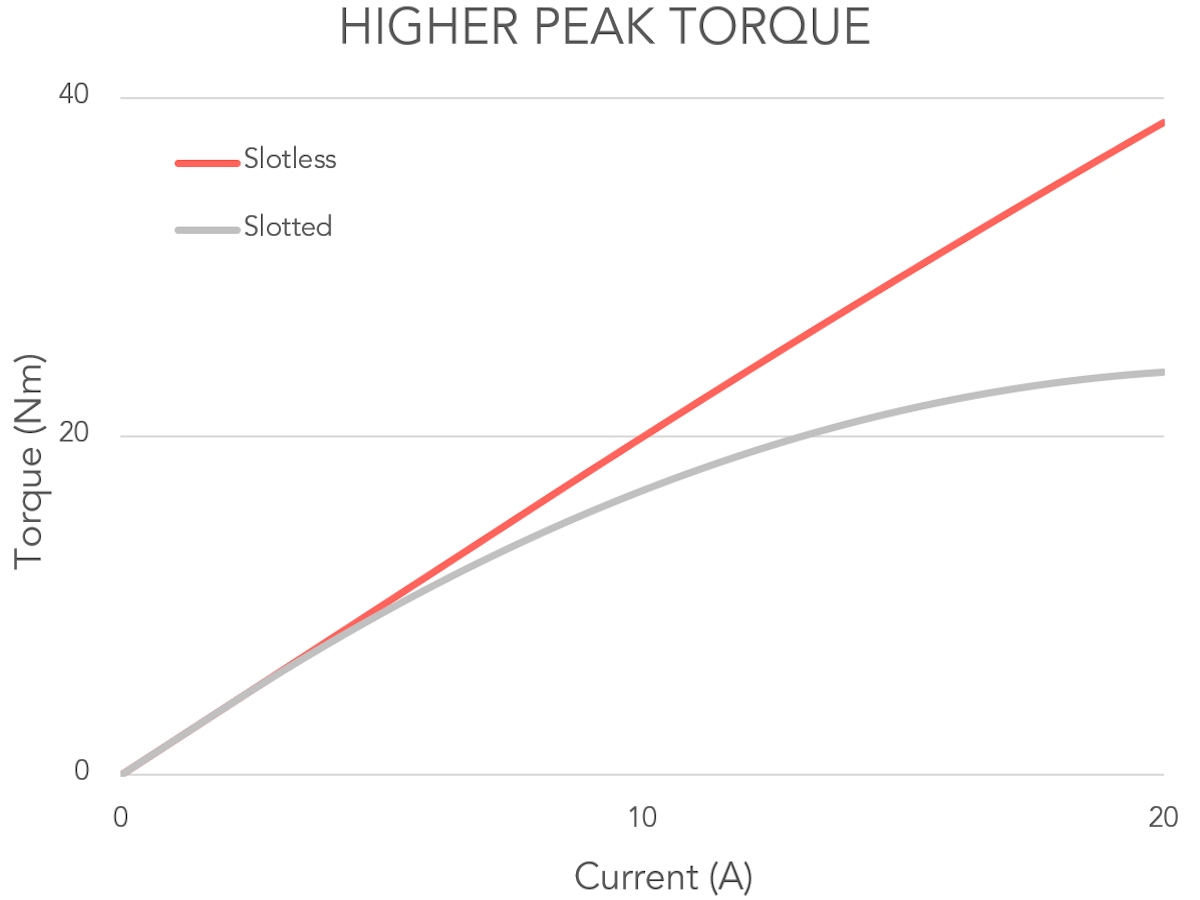
For more information please check: Slotless Motors vs. Slotted Motors
Optimal QDD Robotic Joint Architecture
Joints for lightweight robotics need to be compact. As a result, the joint architecture introduced by MIT for the Mini Cheetah actuator has gained popularity. This design features a gearbox located at the center of the motor, offering substantial size savings. The architecture is based on out-runner motors, which provide a large enough inner diameter to fit the gearbox. However, this introduces cooling and assembly challenges due to the physical placement of the stator and rotor. The design requires a large housing around the rotor to support the bearings on both sides of the actuator.
An in-runner motor, on the other hand, is a better choice for this type of actuator. It eliminates the need for an extra housing and places the stator on the exterior, effectively doubling the conductive cooling surface and significantly improving heat dissipation. However, in-runner motors have historically lacked a large enough inner diameter to meet this requirement.
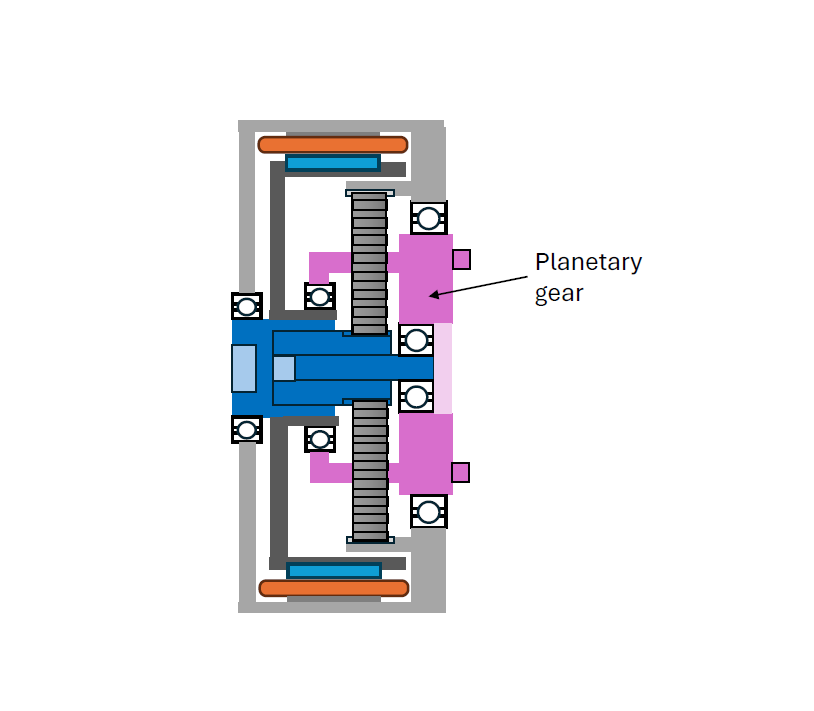
SlimTorq™ Motors for Light Robotics
The Alva SlimTorq™ FiberPrinted slotless motors are an excellent choice for these applications. These motors offer market-leading motor constant density, combining high torque density with enhanced efficiency. The geometrically simple FiberPrinted stator, in combination with the Halbach array rotor, can be optimized to generate an almost perfect sinusoidal back-EMF at all torque levels and temperatures. This results in virtually no cogging torque and higher peak torque capabilities, enabling the highly dynamic, linear current-to-torque behavior required for a high-quality robotic joint.
Additionally, SlimTorq™ motors feature the largest ID/OD ratio, allowing for a compact design that frees up space in the center of the motor, unlike traditional in-runners. This makes it easier to integrate a gear solution, reducing the overall footprint of the robotic joint. Finally, the flexible fiber-printing manufacturing technology enables the motors to be scaled to any size, optimizing performance for each unique robotic joint design. To learn more about Alva SlimTorq™ motors and their applications in lightweight robotics, visit Alva Industries.
Contact
Nicolas Giraudo
Chief Commercial Officer
Fossegrenda 1, 7038 Trondheim, Norway
Our motors
All rights reserved ©2025