Saturation & Peak Torque Capability of Slotless Motors
Explore the advanced torque capabilities of Alva Industries' FiberPrinted™ slotless motors. Learn how they achieve high precision, efficiency, and peak torque through innovative design.
June 19, 2024
.avif)
Conventional electric motors use cores made of ferromagnetic materials to support the winding and increase the magnetic flux density and energy density of the motor. Saturation is the state that ferromagnetic materials reach when an increase in the applied external magnetic field H cannot increase the magnetization of the material further, so the total magnetic flux density B begins to level off. Saturation is most clearly seen in the magnetization curve (also called B-H curve) of a certain material, as a bending of the curve to the right (Fig. 1). The saturation limit is reached at point [B2,H2], however the curve starts leveling off before this, at point [B1,H1].
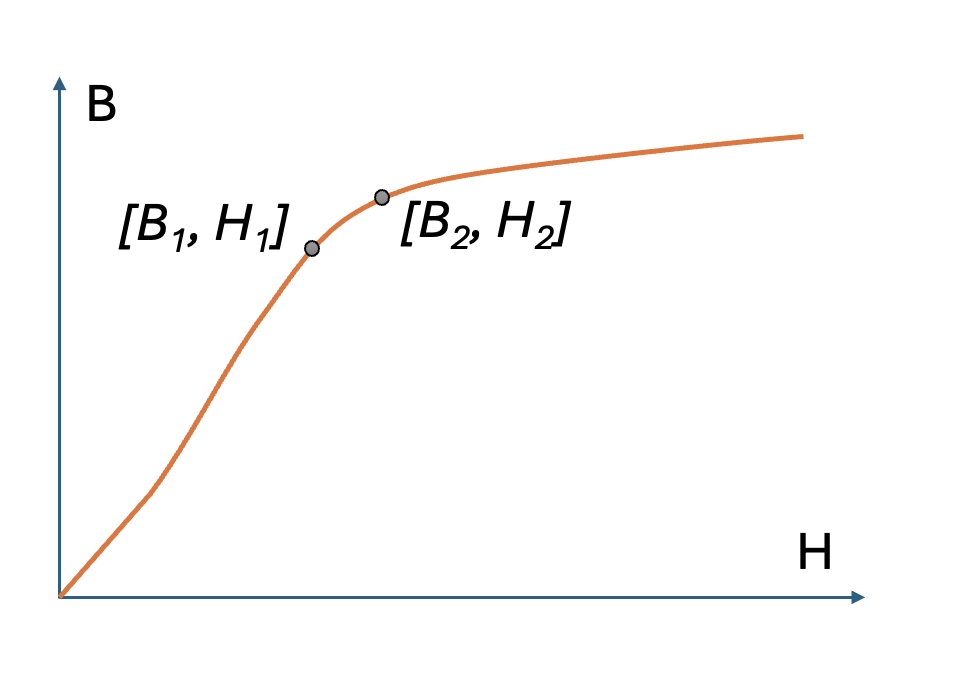
Laminated electrical steel sheets used in electric motor cores are made of ferromagnetic materials; thus, they also experience saturation. Different steel grades experience saturation at different H and B levels – see Fig. 2.
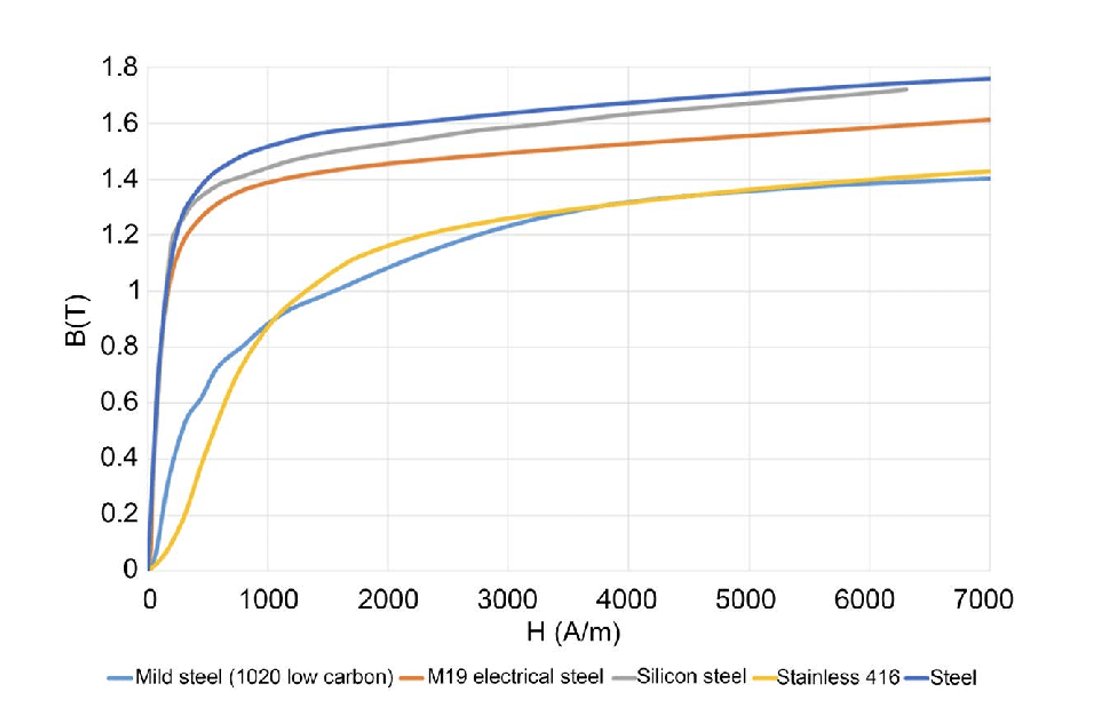
The relationship between H and B can be described as B = μH, where μ is magnetic permeability. Moving along the B-H curve μ changes as shown in Fig. 3. At higher values of H, magnetic permeability decreases towards the magnetic permeability of free space (e.g., vacuum, air).
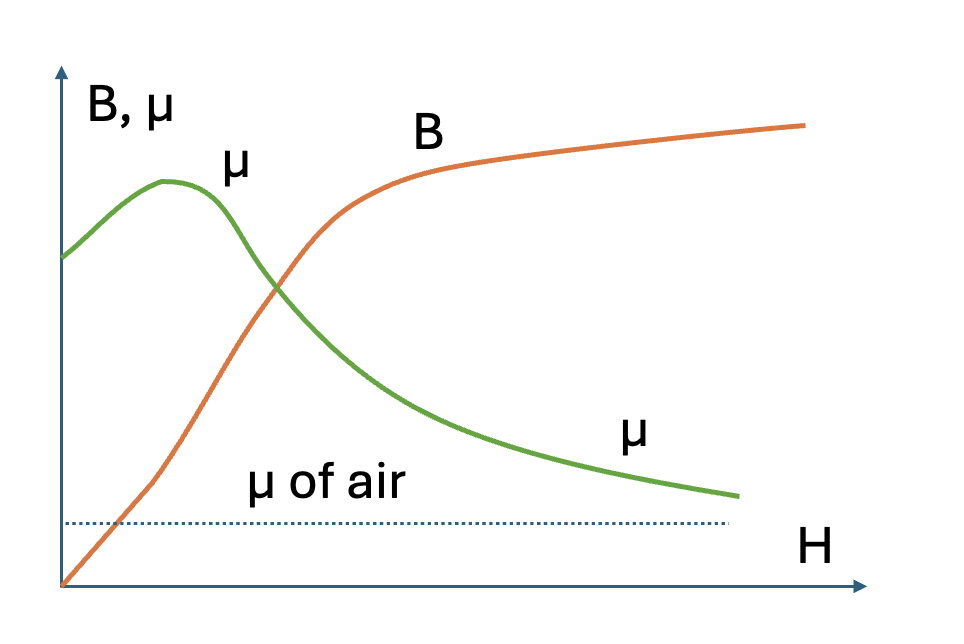
In electric machines, the external magnetic field H is created by the currents flowing in the copper coils; thus, H is proportional to the current. After the saturation is reached when the current increases further, H increases proportionally and permeability of steel μ decreases to the level where steel becomes magnetically equivalent to air. In an actual motor, the teeth bearing the highest currents at some given point in time go into full saturation - see the red domains in Fig. 4 - and in a magnetic sense, they “disappear” as parts conducting magnetic flux.
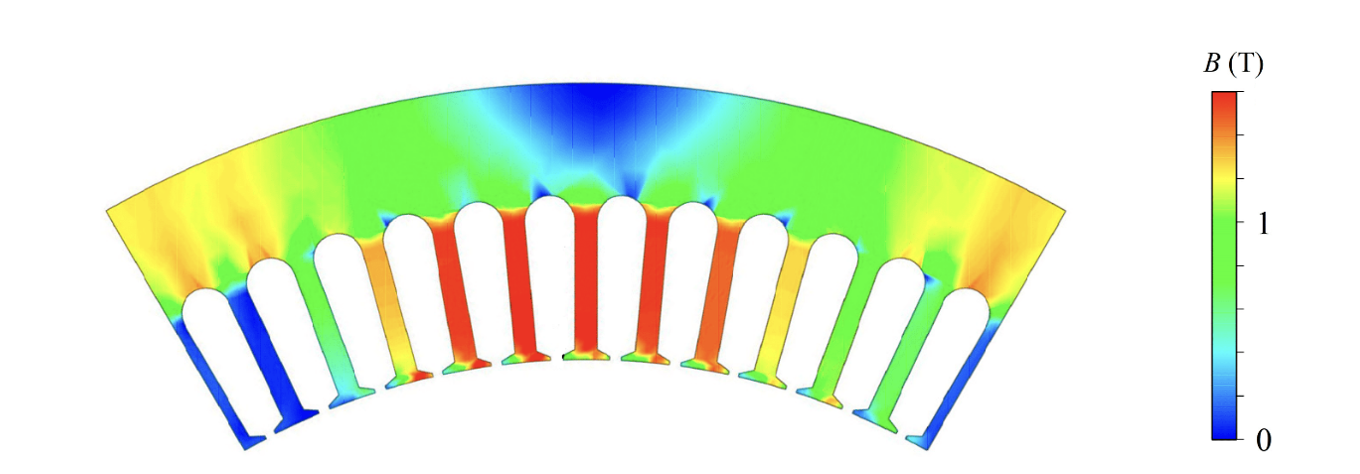
The goodness of the motor, among other factors, is defined by its capability to translate input current into output torque. Linearity of current-torque characteristics is an important figure of merit, since it is easier to control a motor where the torque increases linearly with the current for the entire operating range of the motor. When input current increases, while iron-cored motors saturate and cannot provide adequate torque, slotless motors continue providing increasing torque, proportional to the current (Fig. 5). Thanks to this feature, conventional slotless motors demonstrate comparable or even higher peak torques (with a possible duration of a few seconds) than conventional iron-cored motors.
FiberPrinted™ motors, having a higher copper fill factor and more optimal winding geometry compared to conventional slotless motors, demonstrate higher torque capability than these slotless motors and outperform iron-cored motors in peak torque (Fig. 6).
Modeling shows that even at currents as high as 10 times the rated, the back iron in FiberPrinted™ motors does not saturate. Thus, in practice, Alva motors can be deemed “saturation-free”.
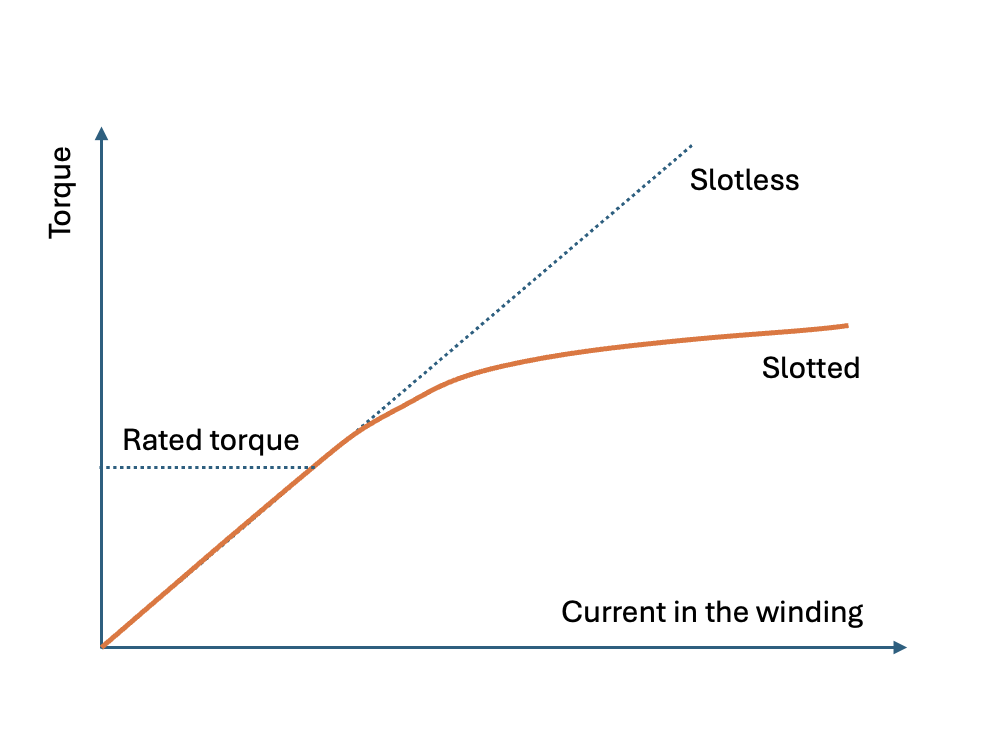
-of-some-motor-types.png)
References
[1] J. Kappatou, G. Zalokostas, D. Spyratos (2016). Design optimization of axial flux permanent magnet (AFPM) synchronous machine using 3D FEM analysis. Journal of Electromagnetic Analysis and Applications. 08. 247-260.10.4236/jemaa.2016.811023.
Read More:
All rights reserved ©2025