FiberPrinting™: The Revolution in the Realm of Ironless and Slotless Motors
Explore how FiberPrinting™ technology is revolutionizing ironless and slotless motors, offering unmatched performance and efficiency. Learn about its impact on the future of motor design.
May 20, 2024
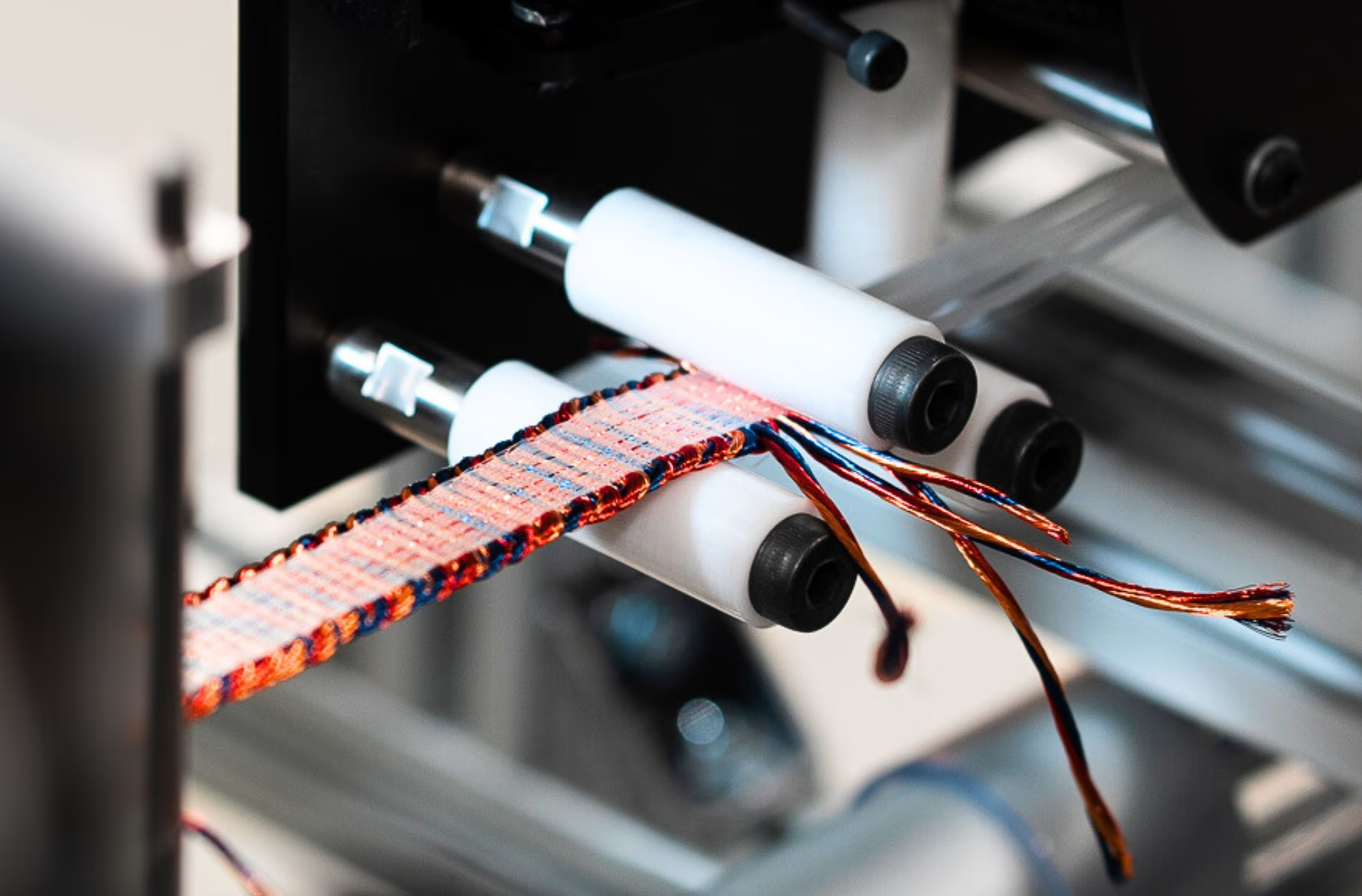
Table of contents
The FiberPrinting™ Process
Form
Mould
Higher Copper Fill Factor and Thinner Windings
Optimal Winding Geometry
Unparalleled Production Efficiency and Flexibility
The Right Technology at the Right Time
Partner with Us
Both slotless and ironless electric machines, motors and generators, employ windings without iron teeth. Alva Industries AS has developed and patented a highly flexible and scalable production method called FiberPrinting™ enabling the appearance of slotless and ironless machines with revolutionary performances. The details of the technology can be found described in several published patents. This text provides just a short summary.
The FiberPrinting™ process is best described in three steps:
1. Print: First, copper wires and structural fibers are combined to form a flat and flexible composite material (Fig. 1). The copper wires inside the material will make up the electrical winding in the finished electric motor or generator.
2. Form: Then, the composite material is formed into a cylindrical shape and placed inside a mould. A stabilising filler material (typically epoxy) is added into the mould.
3. Mould: Finally, the composite material and stabiliser is cured and demoulded (Fig. 2). The result is a self-carrying cylindrical part with integrated copper winding that produces a rotating magnetic field when connected to an AC power source.
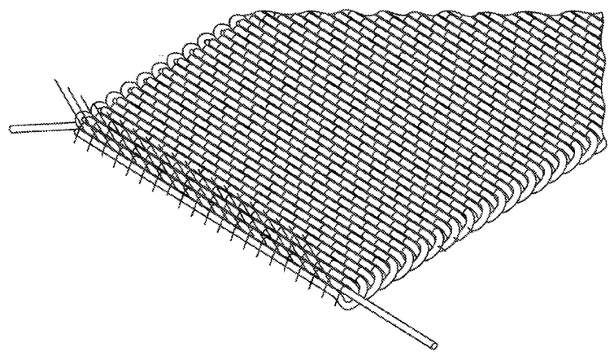
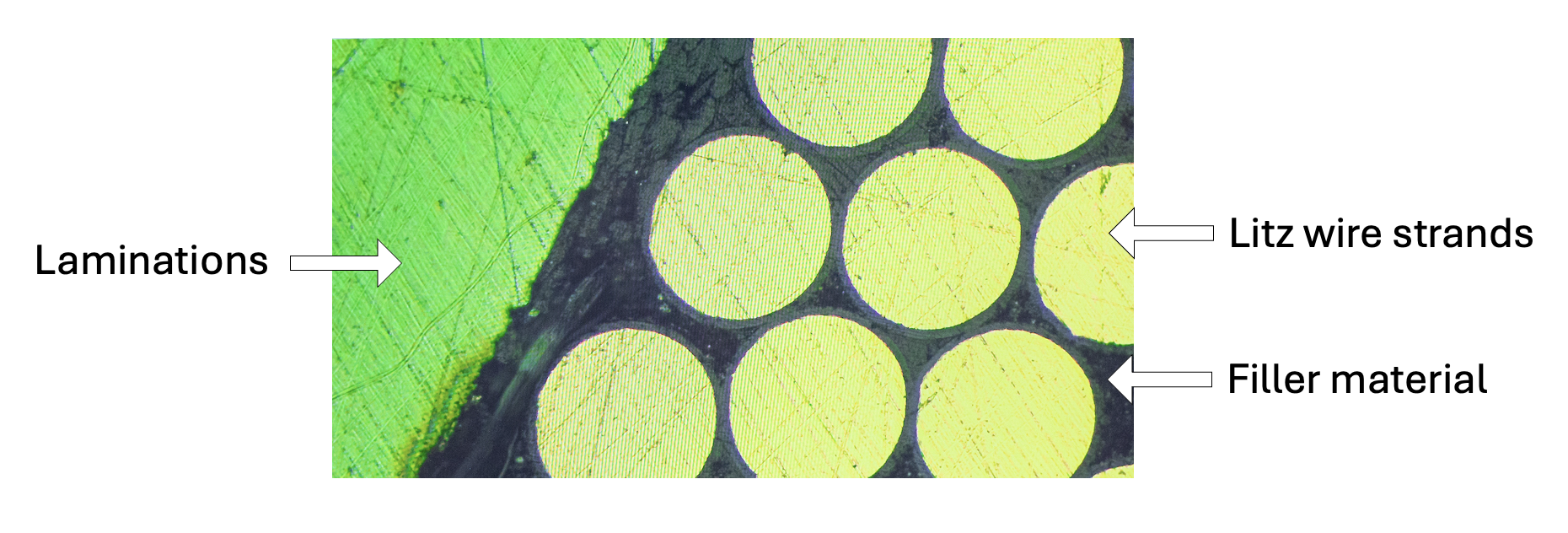
Applying Alva's FiberPrinting™ technology results in essential improvements in product performance which is enabled by two main factors: (1) the ability to make thinner stator than competitors while having the same effective cross-sectional area of copper, reflected in higher Copper Fill Factor (CFF)2; and (2) improved winding geometry inside the stator enabling higher torque production for the same amount of electric current.
Higher copper fill factor and thinner windings
To keep low losses in the copper winding there should be an adequate cross-sectional area of the copper conductors, ensuring low electric resistance. Ideally, all the available area should be filled with copper, which is equivalent to 100% CFF. However, in reality due to the need for insulation between the copper strands, the shape of the strands, and the imperfections of production technologies, only a part of the available area is occupied with copper. Since the required area of copper cannot be reduced to keep the losses low, a low CFF leads to an increase in the total area occupied by the winding resulting in thicker stator designs which in turn results in higher weight of the electric machine and usage of more of the expensive permanent magnet materials.
Conventional production methods utilise one of the two main production processes, both which rely on winding two layers of copper windings together, separated by a middle layer of inactive isolating material.
The two alternatives are:
1. Winding the copper coils around a plastic strip, which then remains inside the winding, taking up space that would otherwise be utilised for copper (the method illustrated in Fig. 3),
2. Laminating precision-etched copper sheets together with a middle-layer of isolating material, before manually soldering the copper sheets together around the circumference of the stator component – again leaving the inactive insulating material in the stator, taking up precious volume where copper would be preferred.
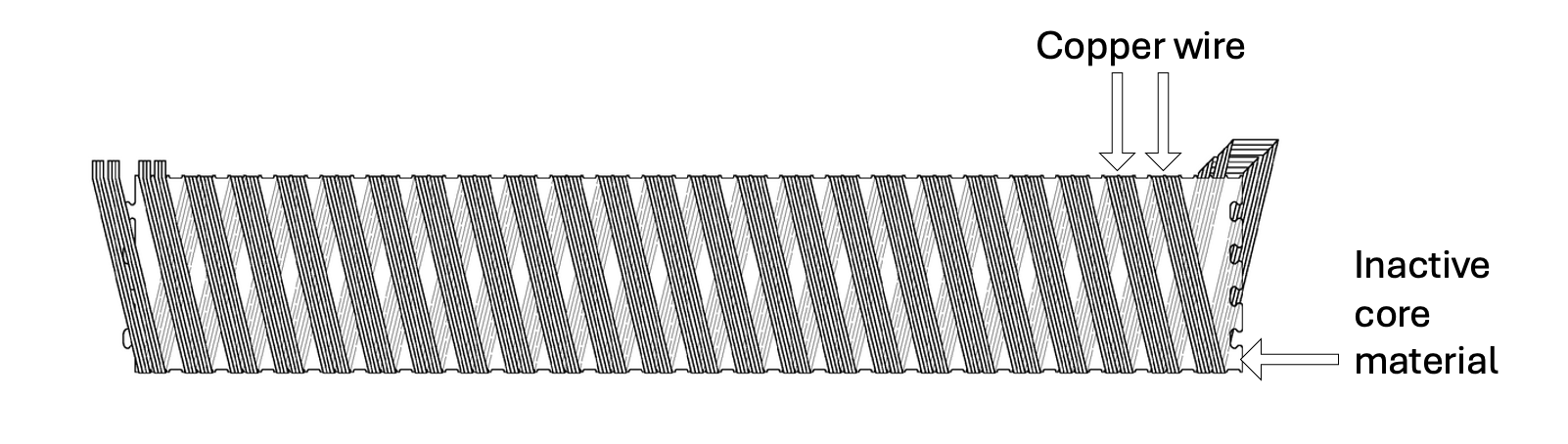
Since both production processes involve an inactive material layer which stays inside the stator component, many of the existing ironless motor manufacturers struggle to increase CFF above 30%. Comparatively, Alva’s technology enables a much higher CFF of >50%. Visually, the difference is illustrated in Fig. 4 comparing across-sectional view of a winding made with conventional methods and using FiberPrinting™ technology. Higher CFF allows making considerably thinner stators which in turn yields a considerable increase in motor torque density.
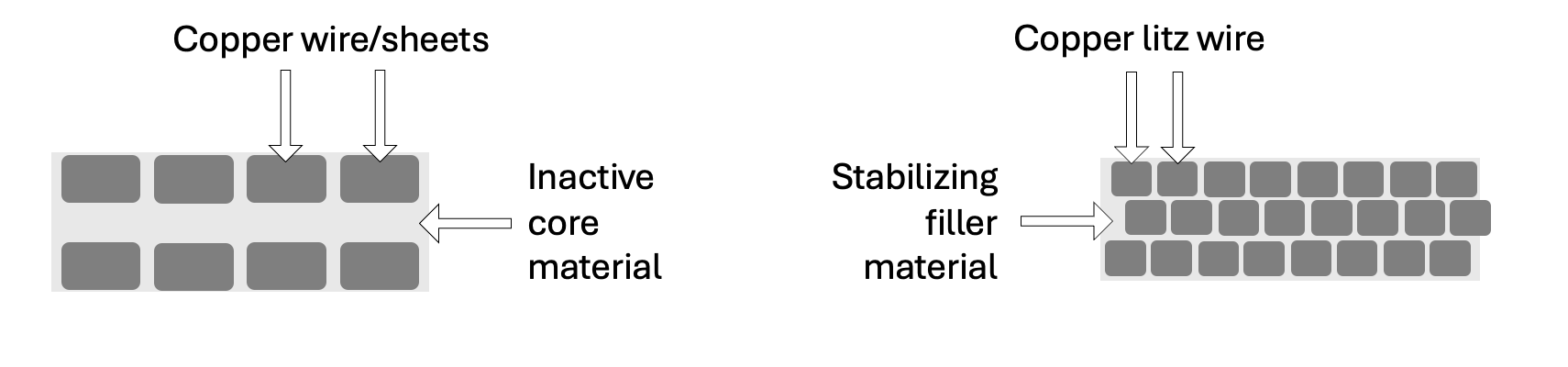
Optimal windings geometry
The second factor contributing to increases in performance of ironless or slotless machines made using FiberPrinting™ technology is the freedom that the production process offers in how the copper windings are formed. Using the previously mentioned legacy production technologies, winding around a plastic strip or using precision-etched copper sheets, both processes force the manufacturer to maintain an angle on the copper windings in order to progress the windings around the circular shape of the stator surface. As illustrated in Fig, 5, the force (F) generated by the coils when interacting with the rotor magnets is proportional to the sine of the angle that the copper coils are wound with. In other words, the ideal winding pattern is to use completely straight windings, which is possible with FiberPrinting™ but not with other production processes.
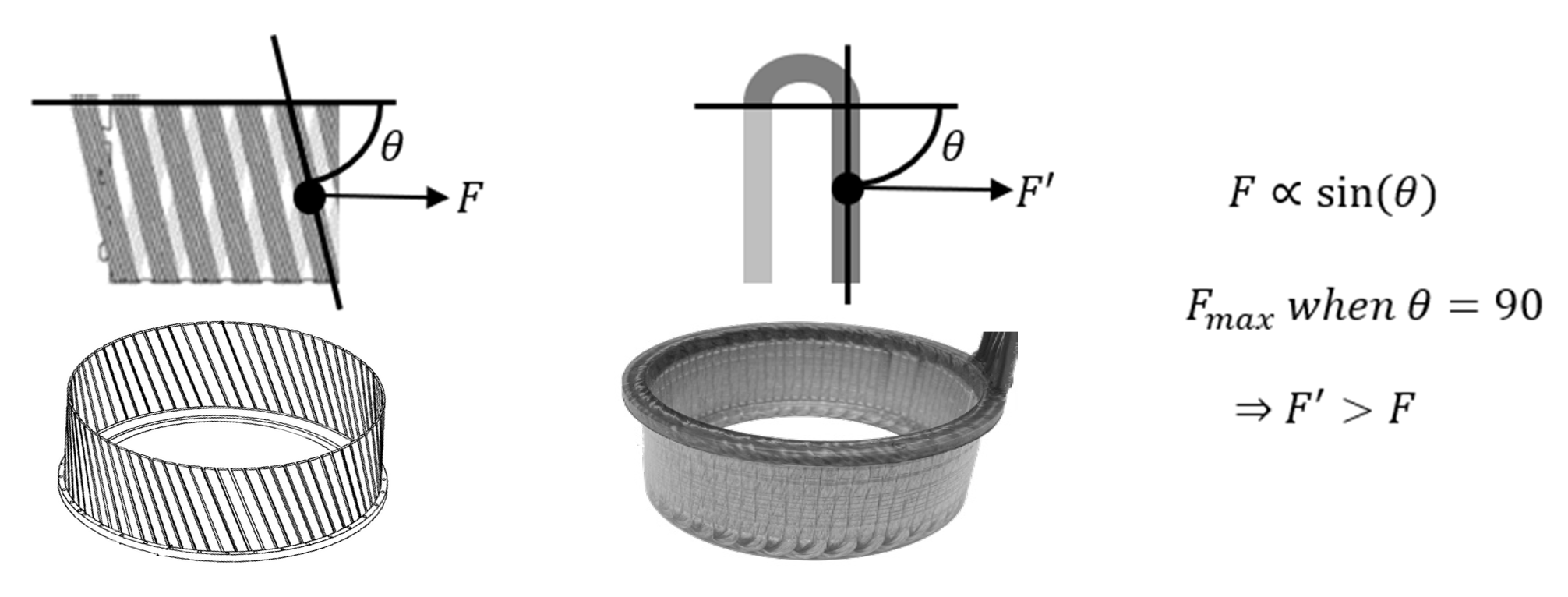
Unparalleled production efficiency and flexibility
Alva’s production technology takes away the time-consuming and labour-intensive work related to the production of the ironless stator component, which is usually the most complex and costly part to manufacture (manufacturing the stator component can make up >60% of production cost of a complete electric motor or generator).
Since each step of the novel production process can be automated and allows for mass-volume production throughput with minimal or no manual labour involved, FiberPrinting™ is probably the first feasible solution to the challenges of manufacturing ironless machines on scale and at a viable cost level.
The FiberPrinting™ manufacturing process is fully flexible to produce a wide variety of windings. This inherent flexibility eliminates the costs of restructuring and retooling the production line for new product dimensions and specifications, which in some cases can cost millions of Euros with conventional production methods (e.g. €15-18 million reported in [3]), since these only allow for one product per production line at a time.
The flexibility of FiberPrinting™ can be compared to the properties of a 3D-printer, where the production line can produce a variety of outputs in different sizes and dimensions, and with different electrical properties, with no adjustments to the production machinery itself. This is explained by examining the initial step of the production process, namely the production of the electromagnetic composite material, and how this material relates to the finished stator product:
1. To change the axial length of the stator component, the FiberPrinter produces a wider composite mat.
2. To change the diameter of the stator, the FiberPrinter produces a longer or shorter mat.
3. To change the electrical properties of the stator, the FiberPrinter uses different copper wires or combines the copper wires in a different winding pattern inside the composite material.
In this way, changing the output of the FiberPrinting™ production line is a simple and effective process of changing the input to the production machinery, and requires no additional retooling or restructuring.
In summary, FiberPrinting™ challenges conventional thinking about how we design and manufacture electrical machines, and offers numerous benefits over legacy technologies in terms of scalability, flexibility and product performance.
The new technology coming in the right time
Alva’s innovation on the production level of lightweight and energy efficient electrical machines has excellent timing with recent innovations in complementing technologies such as power electronics and battery technology, where innovations generally move towards lighter, more compact and more energy efficient solutions.
On a broader perspective, Alva’s innovations are also well timed by making ironless and slotless machines more cost-effective and available as an alternative electric technology, thus accelerating the world’s transition to sustainable and environmentally friendly electric solutions.
Partner with us
At Alva, we are committed to making our innovative FiberPrinting™ technology accessible to a wider market. We are open to licensing our manufacturing technologies to enable other companies to produce high-performance slotless motors utilising their own supply chains and production capabilities. This collaborative approach not only helps in scaling the production of energy-efficient electric machines but also fosters innovation and adaptation across the industry.
We welcome opportunities to cooperate and form joint ventures with companies interested in leveraging our technology. Our team is dedicated to supporting partners through the development of products, initial production runs, and the setup of production equipment at partner facilities. Contact us for more information.
Stay tuned...
In addition to our collaborative efforts, we are continuously expanding our portfolio of Alva Standard products. Our highly customizable solutions are designed to meet the diverse needs of our clients. Stay tuned as we introduce new sizes and configurations that maintain the high performance and flexibility that FiberPrinting™ is known for.
References:
[1] Patent US11646645B2 “Electromagnetic mat for a stator or rotor component of an electric machine”.
[2] Patent US9425664B2 “Composite stator for electromechanical power conversion”.
[3] A. Kampker, P. Burggräf, C. Nee, Costs, quality and scalability: Impact on the value chain of electric engine production, 2012, 2nd International Electric Drives Production Conference, EDPC 2012 - Proceedings.1-6. 10.1109/EDPC.2012.6425089.
1 With removed numberings.
2 CFF is a measurement of the amount of copper per area/volume in the stator component, and largely determines the performance of the electrical machine. Higher is better.
3 With arrows and text added by Alva.
All rights reserved ©2025