Choosing Actuators for Surgical Robotic Joints
Discover how choosing the right actuators for surgical robotic joints enhances precision and control in complex procedures. Learn about the benefits of compact torque motors and how FiberPrinting™ technology optimizes size, power, and customization for next-generation surgical robotics.
November 10, 2024
.avif)
Robotic surgery is becoming increasingly popular because it enables surgeons to perform complex procedures with more precision and control, leading to a variety of patient benefits. The initial scepticism around having a “robot operate on me” continues to reduce, thanks, in part, to the emergence of other robotic solutions in our daily lives whether it be a humanoid serving your drink in a bar or a mobile robot delivering your groceries.
A key element influencing the overall performance and capabilities of the surgical robot is the design and make-up of its joints. Due to different design priorities, there are variations in most current systems on the market. This is reflected in the technical specifications and aesthetic design. Although there are these variations, there are some aspects of the system that nearly all manufacturers are trying to improve including size, safety, speed and power consumption (efficiency).
This paper reviews different design approaches for the robotic joints and introduces a new technology that is being increasingly adopted by surgical robotic manufacturers.
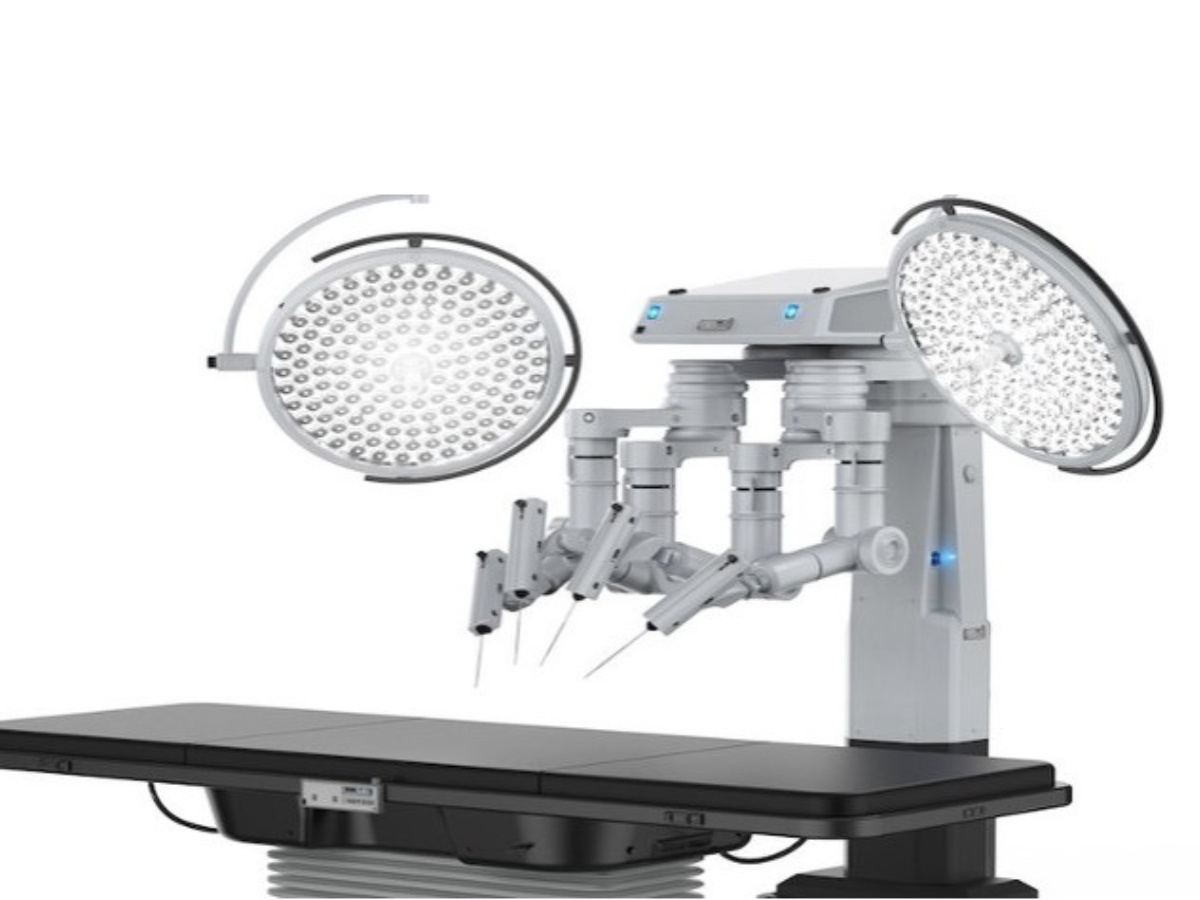
Actuators in Surgical Robots
There are several types of actuation technologies used in surgical robotic systems. There are also several companies that promote off-the-shelf actuators with fixed specifications. The off-the-shelf solutions can be useful for robotic manufacturers producing an initial prototype or first-generation system as they can reduce the development time. However, in the long-term, such solutions are usually designed out as the manufacturers look to reach a higher level of integration to meet a more specific set of specifications aligned to required performance and unique selling points of the system.
What’s in a robot joint?
A robot joint is made up of several components that enable controlled movement. The types of components can vary but typically include a motor, a gear/reduction in form of a gearbox, encoders, bearings, eventually torque sensors, a brake and a servo drive.
This article will focus on the primary mechanical components: the motor, gears/reduction and brake.
Gears
In a robot joint, gears are used primarily for transmitting torque and controlling the motion of the joint. Gear ratio refers to the relationship between the number of teeth on two meshing cogs or the relative speeds of rotation between those gears. It indicates the extent to which a motor’s torque is increased or reduced.
The gear ratio is typically expressed as the ratio between the number of teeth on the driven gear (the gear receiving power) to the number of teeth on the driving gear (the gear providing power), or it can be represented as the ratio of their rotational speeds.
There are different technologies available for the selection of a gear for a robot joint, and the selection will depend on the desired specifications for the robotic application. Robotic solutions in surgery are typically serial kinematics. In serial kinematic solutions the torque required in the bigger axes is quite elevated and therefore the gear ratios tend to be very high. In these applications strain wave gears are typically used.
Motors
One of the factors impacting gear selection is the type of motor technology used in the joint. The strain wave technology is most common when using frameless motors as the driving technology, which is the motor technology selected when compactness is important.
When using other motor types, other gear technologies are more suitable, like the very common integration of worm gears with BLDC motors.
Frameless torque motors provide many design advantages with regards to compactness, controllability, weight reduction and performance. Torque motors can also provide a higher torque than regular BLDC motors, which allows for a lower gear ratio or, in some instances, no gearing at all (see later). The lower the gear ratio the easier it is to back drive as well as improved efficiency, greater sensitivity and transparency (i.e. the ability to sense torque with the current applied to the motor).
Brakes
One of the challenges of reducing the gear ratio is related to the brakes. Serial kinematics require a brake in almost all axes, with some exceptions sometimes like the end effectors or axes that only move horizontally (perpendicular to gravity). If the gear ratio is reduced, the brakes would have to be able also to produce a higher braking torque which, depending on the technology used in the brakes, could mean also bigger sizes and increased weight. This would ultimately contradict or work against the aimed weight and size reduction of motors and gears.
Electromagnetic brakes, however, have improved in recent years and very light brakes can now provide a high braking torque while also being scalable and customizable.
Using Direct Drives in Surgical Robots
Not all axes of a surgical robot joint require geared actuators. An end effector or the “wrist” can also be solved by using a torque motor with no reduction. A direct drive solution in these types of applications can provide several benefits in terms of size and weight reduction, high dynamic performance and lower cost. See A Guide to Torque Motors to learn more.
If torque motors offer such benefits, one might ask why manufacturers do not design a whole robot with no gears, and just use direct drives. Some parallel kinematics have shown that this design is feasible, however, for serial kinematics this solution is uncommon, due to the lack of robustness that such a system would have, which is an issue for systems that require high stability.
Precision Torque Motors with FiberPrinted™ Technology
Integrating torque motors into a geared actuator, requires careful consideration. A growing trend in the surgical robotics industry and other precision applications, is to use precision torque motors manufactured with FiberPrinted™ technology.
FiberPrinting™ is an industrial winding method that allows for continuous winding of stator mats for ironless and slotless motors.This method maximizes copper fill factor and enables precise customization of size & stator configuration, resulting in the optimal combination of torque density and precision in a thin and lightweight form factor.
These ultra-thin motors allow for a complete integration inside a gearbox (concept expressed in Figure 3) and their coreless design also enables the torque motors to operate at higher speeds.
Further information is available in this article: Slotless Motors vs. Slotted Motors: What is the difference?.
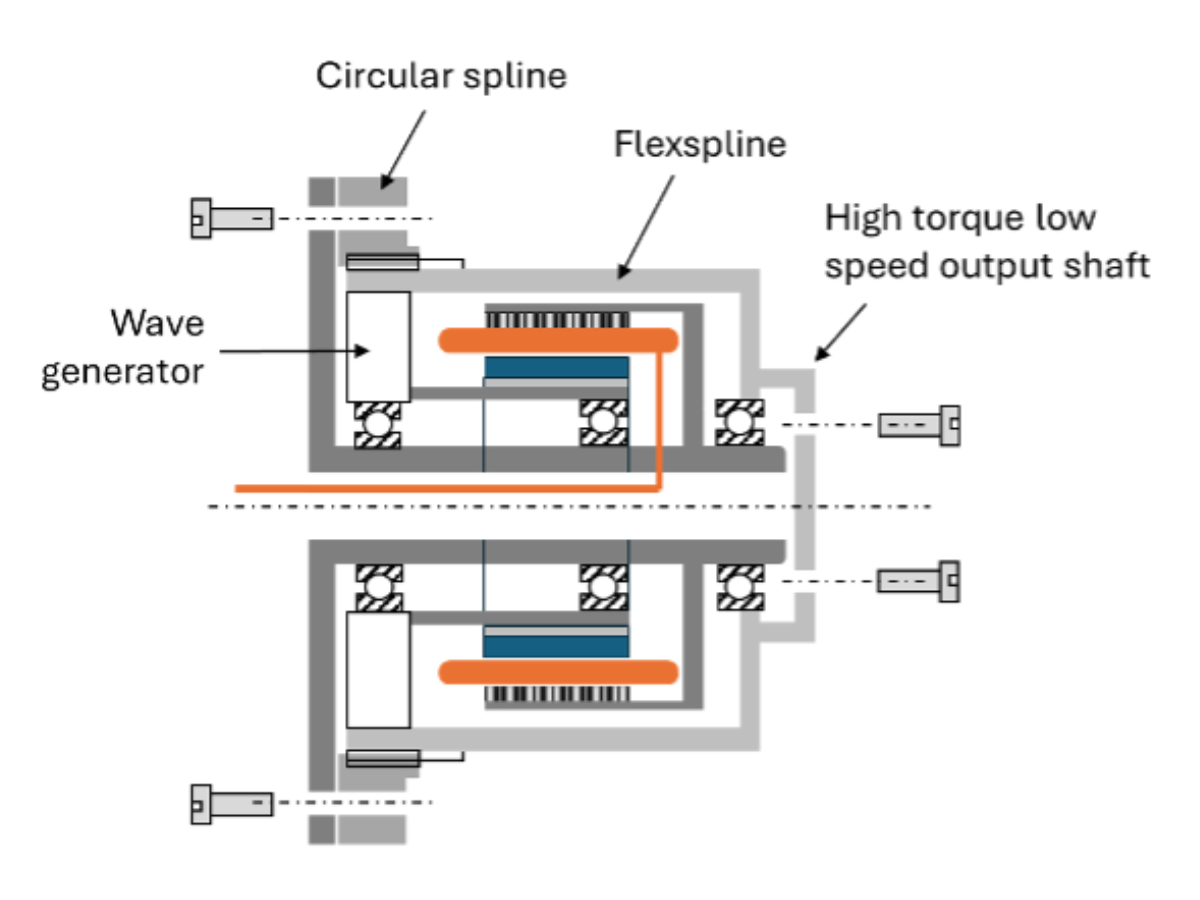
.png)
The ability that FiberPrinting™ provides to integrate compact solutions results in several benefits, not only to the mechatronics designers, but also the surgical robot manufacturers and end-user surgeons. As shown in Figure 3 below.
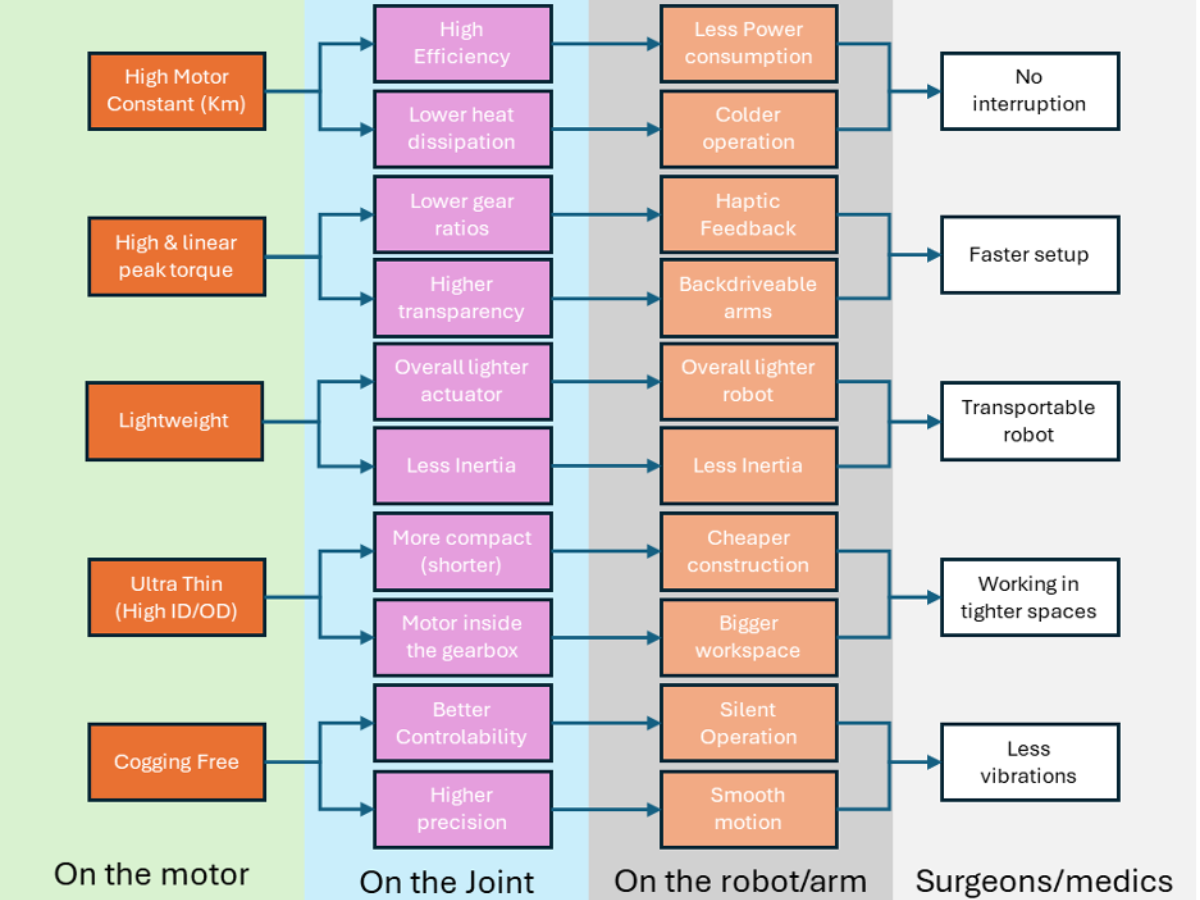
All rights reserved ©2025