An Engineer's Guide to Frameless Motors
Everything you need to know about frameless motors, including how they work, how they compare to framed motors, their advantages & applications.
August 20, 2024
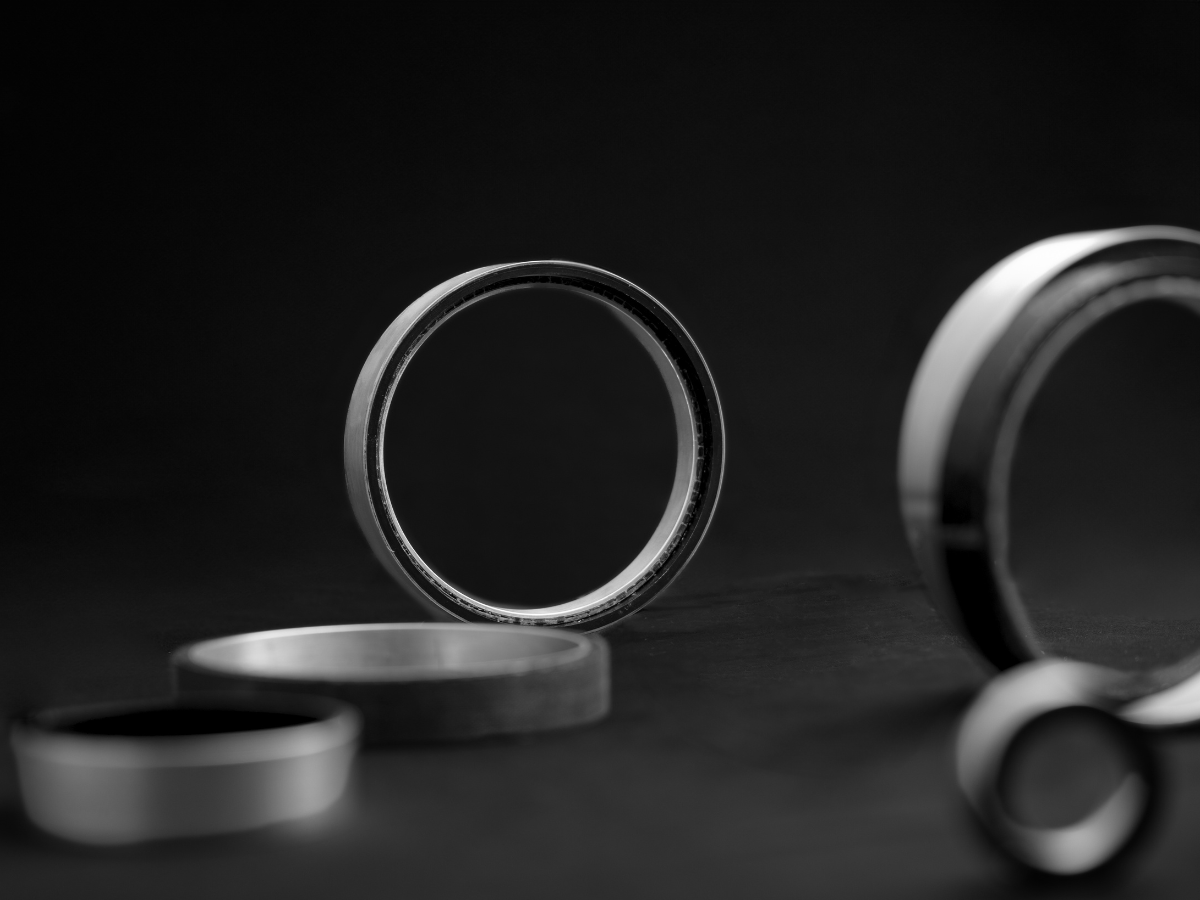
Choosing a frameless motor for your motion control project can give you higher design flexibility and a higher performance system. Unlike traditional packaged or framed motors, frameless motors are designed to be integrated directly into the mechatronics of the machine or device they power. Understanding what frameless motors are, when to use them, and how to pick the best frameless motor for your needs is key to unlocking their full potential.
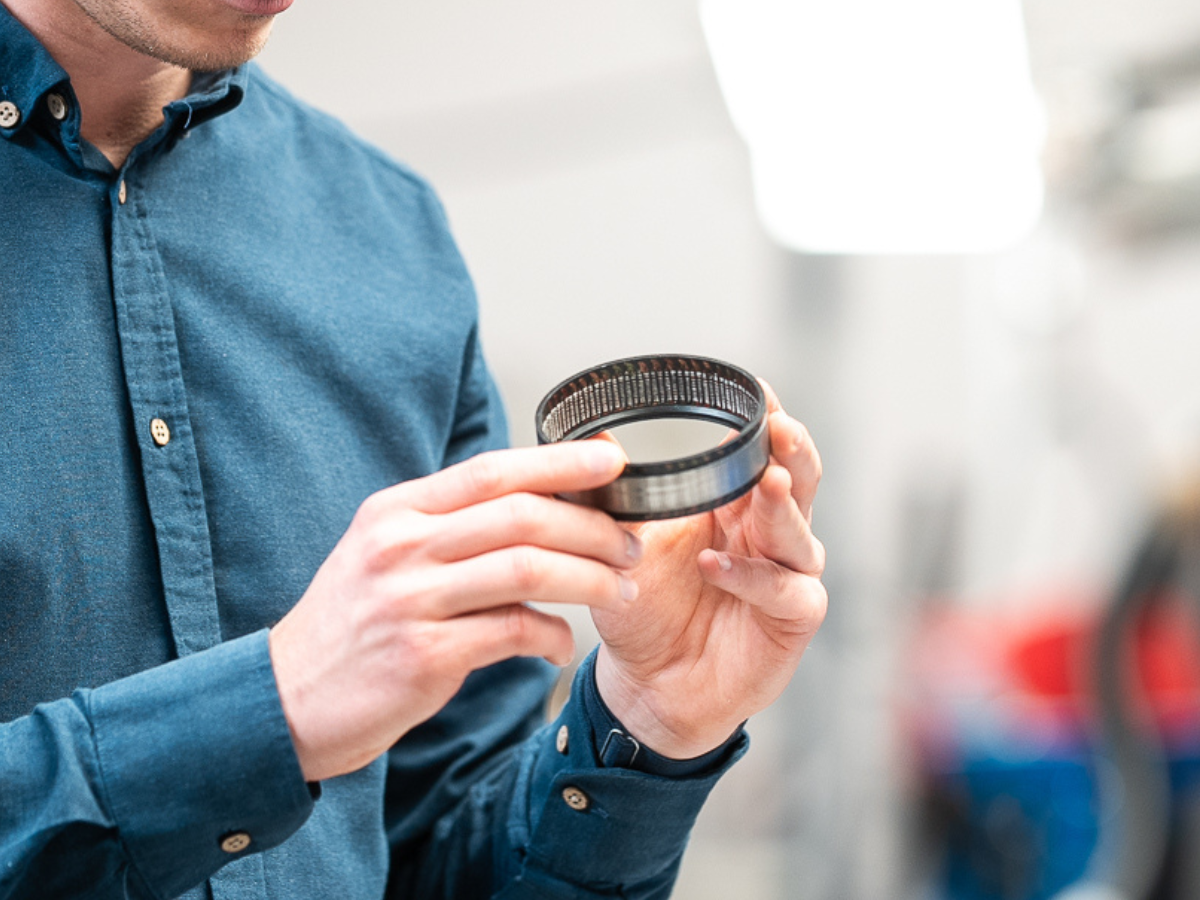
What is a Frameless Motor?
Frameless motors, also known as motor kits or torque motors, consist only of the rotor and stator. They do not include a housing, shaft, or bearings. This allows engineers to use the host equipment as the housing as well as the host’s own shafts, seals, and bearings. Thus, motor integration can be better optimized for cost, weight, efficiency, size, or heat dissipation. When designing custom solutions, frameless motors are especially adequate.
How Do Frameless Motors Work?
A frameless motor operates on the same principle as framed brushless motors, by converting electrical energy into mechanical motion. The copper windings in the stator produce a magnetic field that pushes or pulls on the magnets on the rotor, producing a rotating motion. A motor driver is used to control the alternating electric current fed into the stator, producing an accurate, precise, and efficient torque and speed output.
A frameless motor is designed to be integrated into the host’s mechanical system. The rotor is typically attached to a rotor shaft or to the moving part of the system, and the stator is attached to a housing or the static part of the design.
Features of Frameless Motors
Frameless motors offer several key features that make them suitable for high-performance motion applications:
- Compact Design: Integrating the frameless motor into the motion system allows the design of a compact system.
- Direct Integration: The absence of a frame allows for direct integration into the mechanical system, reducing assembly complexity and improving overall system efficiency.
- Customization: These motors can be tailored to specific application needs, such as custom rotor and stator sizes or specific winding configurations.
- Improved Dynamics: With fewer components and optimized integration, frameless motors typically offer improved dynamics.
- High Torque Density: Frameless motors deliver high torque in a compact package, which is crucial for applications requiring powerful and precise movement.
- Cost Efficiency: No need to pay for unnecessary motor housing, shaft, and bearings.
Applications of Frameless Motors
Frameless motors are used in a variety of high-performance and specialized applications, including:
- Robotics: In robotic arms, frameless motors provide the precision and torque needed for complex movements in a compact form.
- Aerospace, Ground and Marine: Due to their lightweight design, frameless motors are used in avionics, drones, gimbals, and other aerospace systems as well as in systems on ground and marine vehicles.
- Medical Devices: Frameless motors are ideal for surgical robots and other medical equipment where space is limited, and precision is paramount.
- High-precision Mechatronics: For verticals like metrology, machine tooling, material processing, and others, frameless motors allow for very compact designs with high precision.
- Industrial Automation: Frameless motors are well suited to drive direct-drive systems that require high torque and precise control in a small footprint.
- Electric Vehicles: Frameless motors are often used in in-wheel motors and other automotive applications where integration and performance are essential.
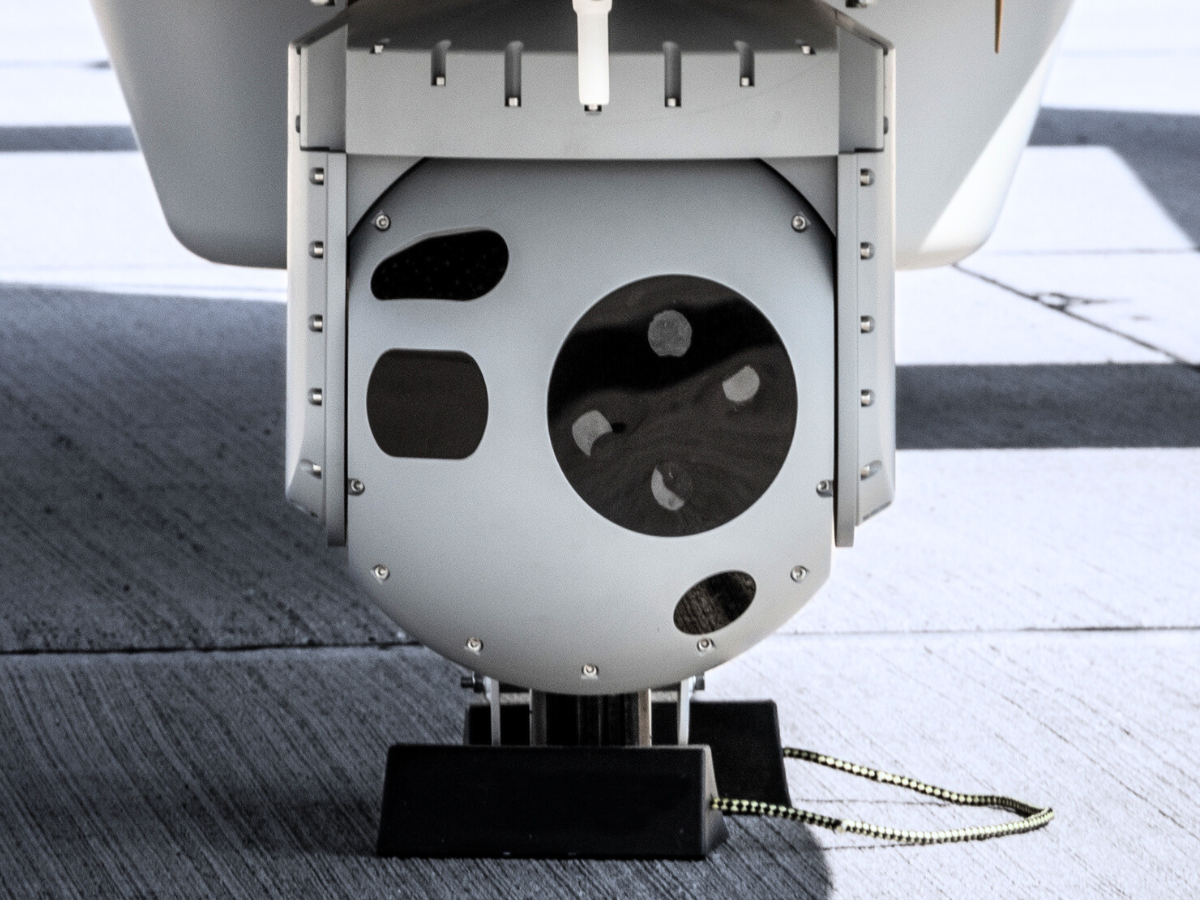
Main Selection Criteria for Frameless Motors
When selecting a frameless motor for a specific application, engineers must consider several factors:
- Required torque and speed: Understanding how hard the motor needs to push and pull, and at which speeds, is one of the key factors to choosing a motor.
- Thermal management: Considering the maximum allowed temperature and the cooling conditions of the motor is important to know how many losses the motor can have at the given operating points.
- Space constraints: The frameless motor can be integrated directly into the system, so knowing the maximum size the motor can have is important.
- Weight: The overall weight of the system also needs to be considered when selecting the right motor technology. There are also technologies for making frameless motors that are lighter than others (e.g., slotted vs. slotless).
- Supply voltage and maximum input current: Being a part of a system, and using a motor controller, some constraints on the supply voltage and input current may already be set before choosing the frameless motor.
- Precision requirements: How precise the motor needs to be to perform the intended tasks. Maybe a zero-cogging motor is needed.
- Other components in the system: Even though the selection of the motor is one of the most important aspects of the design of the motion system, the rest of the components must work together with the motor as well. The flexibility of the frameless motors technology allows for compatibility with most components forming the motion system.
Frameless motors offer a highly flexible and high-performance solution for a wide range of applications. By understanding frameless motors, and the key selection factors, engineers can design the optimal solution for their system. Whether it is aerospace, medical devices, or robotics, frameless motors will continue playing a critical role in the advancement of technology.
What Are the Benefits of Frameless Motors?
Frameless motors give engineers greater design freedom by removing the constraints of a pre-defined housing. This opens the door to more compact, lightweight products, since the motor can be fully integrated into the surrounding structure. With the stator and rotor delivered as separate components, you have full control over the bearing system, selecting the type and quality best suited to your application. The motor housing can often double as part of the main mechanical assembly, reducing part count and simplifying the overall system. Additionally, the open center design provides valuable space for integrating gearboxes, cabling, slip rings, or other components, making frameless motors an ideal choice for high-performance, tightly packaged systems.
Frameless Motors vs Traditional Motors: What’s the Difference?
The key distinction between frameless and traditional motors lies in their level of integration. Frameless motors consist solely of the rotor and stator, along with the functional core of the motor, allowing engineers to embed them directly into the mechanical structure of a system. Traditional motors, often referred to as housed motors, BLDC motors, or servo motors, come as complete units with a built-in housing, bearing system, and shaft. This makes them ready to mount and operate out of the box, but limits flexibility in terms of size, weight, and component layout. Frameless motors, on the other hand, require more upfront design and assembly effort but enable highly optimized solutions: you choose the bearings, define the mechanical interface, and can achieve a much more compact and integrated final product. This makes frameless motors particularly attractive in applications where space, performance, and weight are critical.
How to Integrate Frameless Motors into Your System
Integrating a frameless motor requires thoughtful mechanical design, but offers unmatched flexibility in return. There are several reliable methods to secure the stator and rotor within your assembly, depending on your performance, thermal, and serviceability requirements. Bonding, either with a small or large gap, provides a simple and effective solution, especially in space-constrained designs. For applications demanding easy assembly and disassembly, axial clamping offers a non-permanent yet secure alternative. In cases where a rigid interference fit is desired, a press fit can ensure precise alignment and excellent thermal conductivity. Each approach has its own trade-offs, but all allow you to tightly integrate the motor with your mechanical system, improving overall compactness and performance.
Frameless Motor Performance and Efficiency Explained
Frameless motors are typically selected for applications where torque output is more critical than overall power. Because they’re integrated directly into the mechanical system, the performance optimization starts with the motor constant (Km). By maximizing the motor constant within given mass or space constraints, designers can achieve higher efficiency, reducing copper and core losses, minimizing heat generation, and lowering power input for a given torque. The goal is to deliver the maximum continuous torque while keeping the system compact, lightweight, and thermally stable. This makes frameless motors particularly well-suited for high-performance applications such as robotics, medical devices, and aerospace systems, where every gram and every watt matters.
Tips for Optimizing Frameless Motor Performance
To get the most out of a frameless motor, it’s essential to start with a clear understanding of your application’s torque and speed requirements. The precise definition of these parameters ensures the motor is correctly sized and prevents overspecification, which can lead to unnecessary bulk or inefficiency. Next, pay close attention to the torque constant (Kt) - choose a motor whose Kt aligns with your target speed, torque, and input voltage. In general, a higher Kt means better efficiency and thermal performance. It’s also beneficial to select a motor with the highest possible motor constant (Km) within your mechanical constraints, as this directly impacts how efficiently torque can be generated. Finally, pair the motor with a driver tailored to your application, whether that’s a precision controller for smooth, accurate motion or a performance-oriented drive for dynamic, high-torque systems. A well-matched combination of motor and electronics will unlock the full potential of your frameless motor integration.
Nicolas Giraudo
Chief Commercial Officer
Fossegrenda 1, 7038 Trondheim, Norway
All rights reserved ©2025